Czech carmaker Škoda Auto has turned its prototype lab into a factory for respirators. The idea to use 3D printers to make respirator parts came from the firm’s scientists and technicians. There is a critical shortage of high-quality respirators for medical and emergency staff on the front lines of the coronavirus crisis.
The reusable respirators, intended mainly for doctors, can be made using specific types of 3D printers, and they meet the highest-level protection criteria. They were developed by the Czech Institute of Informatics, Robotics and Cybernetics (CIIRC) of the Czech Technical University (ČTUV).
The entire process, from development and certification to getting production running, took a week. As Škoda owns one of the few 3D printers in the Czech Republic capable of making the respirator parts.
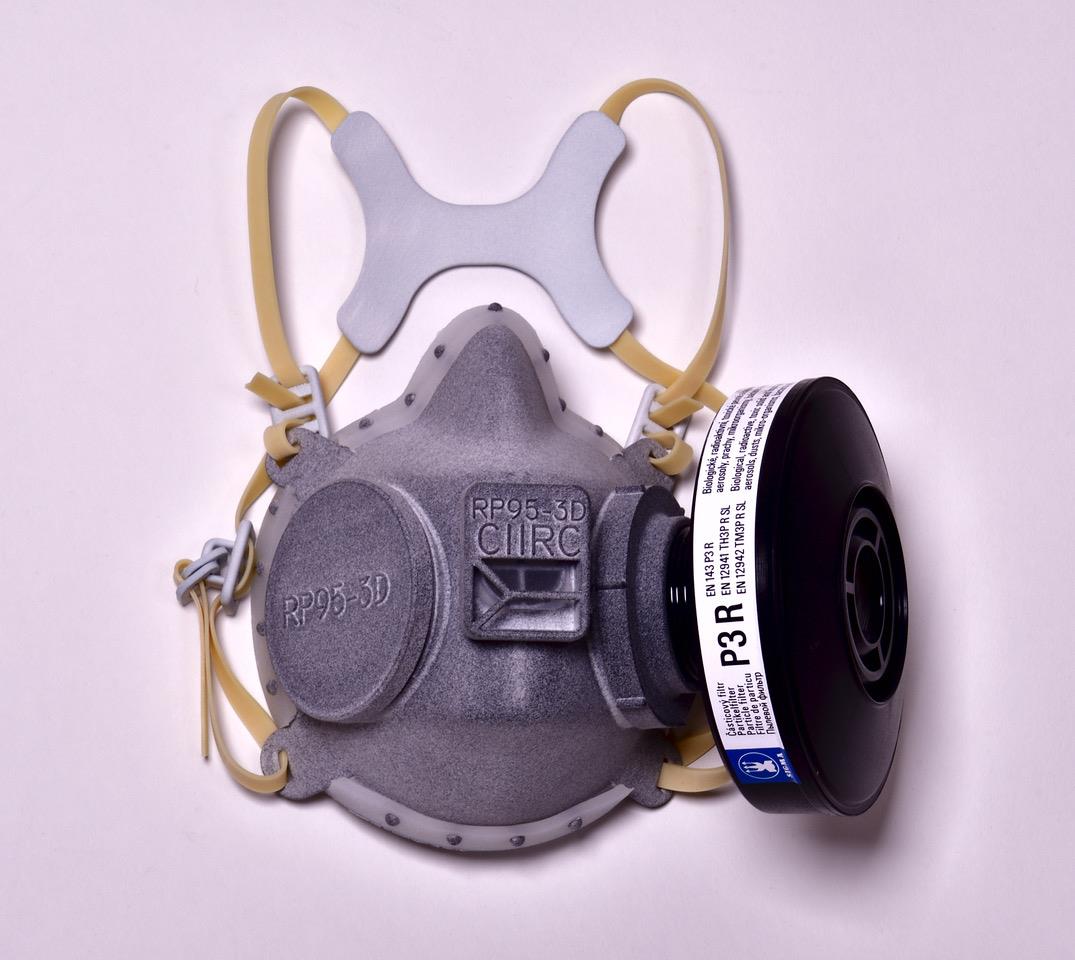
Škodapoints out that any company with one the three types of Multi Jet Fusion 3D printer can also produce CIIRC RP95-3D respirators. They just need to contact the specialists at ČTUV.
“The Czech Technical University opted for Multi Jet Fusion using the polyamide PA-12. This printing method ensures you get a homogeneous material that does not have distinct layers and is not porous. That is key, because it means traces of the virus do not remain in it and it’s easy to disinfect,” David Vaněk, head of the prototype and model construction department at Škoda, said on the company website.
Vaněk and his team began by making five test prototypes. After the process was gradually optimized, the Škoda 3D printer can now print 60 units in a single batch. The use of professional quality 3D printers is important for certification.
“Everything was fine-tuned so that the respirators in a print batch were as close as possible without affecting each other so that the printing process was as efficient as possible,” Martin Sova, coordinator of plastics production and the 3D printing competence center in the prototype construction department, said.

Printing one batch takes 16 hours, followed by a cooling phase that takes roughly the same amount of time.
The respirators are printed in layers, as the polyamide powder is fused by infrared light. In the first step, a layer of powder is spread across the work bed. “Then the print head sweeps across the layer, emitting two substances that basically draw the next layer of the finished part. Then an infrared heater sweeps across it. The powder reacts with the substances to create a solid material,” Sova said. In the next step, the work bed moves down in the print box by the thickness of one layer, and this is repeated over and over again.
After completion, the printed parts are left to cool, as the infrared light fusion temperature can reach 180 degrees Celsius.
The respirators have four parts: the main masks, seal caps, the filter cartridge attachment adapter and exhalation covers. The firm 3Dees collects the components from all the suppliers and makes the final assembly. The filters remain functional for up to a week.
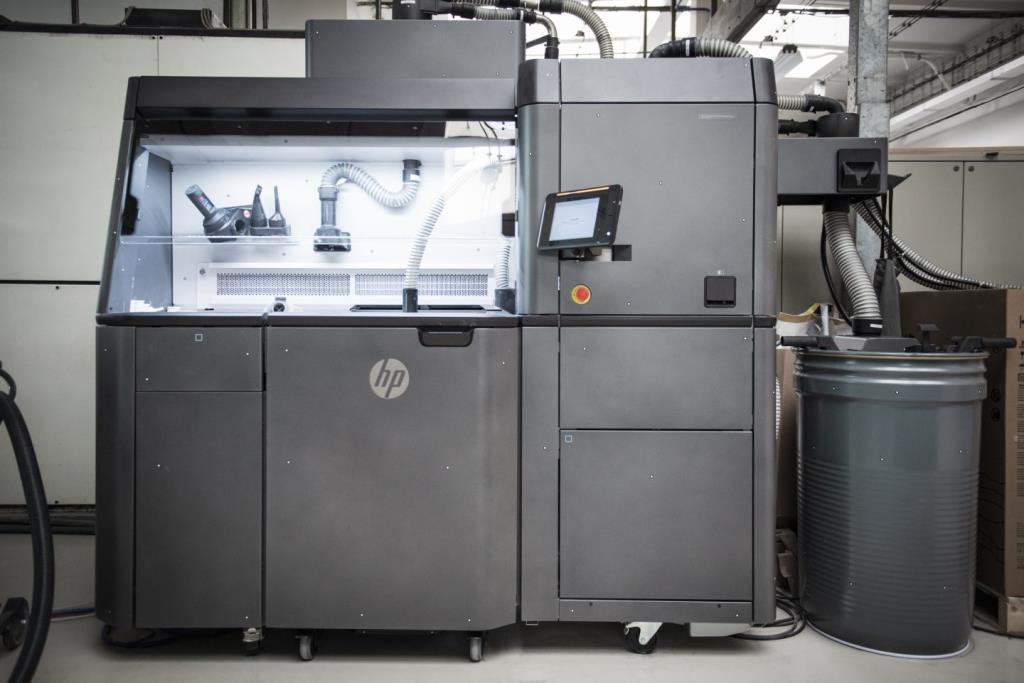
The finished respirators, which can be disinfected and reused, are then sent to the health ministry, which manages their distribution.
The next goal is to start mass-producing respirators. This will require plastic injection molds, which take several weeks to prepare. That’s why 3D printing is currently the best option for providing respirators quickly.
“We will keep supplying our 60 respirator sets a day for as long as they’re needed,” Vaněk said. Only when the situation allows will the 3D printer revert to its usual job of producing parts for Škoda.
Škoda is the largest private employer in the Czech Republic, accounting for some 5% of national GDP. The carmaker was founded in 1895 as Laurin & Klement. It is headquartered in Mladá Boleslav, in Central Bohemia. In 1925 Laurin & Klement was acquired by Škoda Works, which became state owned in 1948 and was privatized after the Velvet Revolution. It is now a subsidiary of German carmaker Volkswagen.